The friction of the wire in the conduit is caused by the fact that the wire rests against the inside of the tube. This grows exponentially with the bending angle and, depending on the coefficient of friction rapidly to a complete blocking of the wire electrode.
The electrically driven feed assist RoboFeed exerts a permanent and continuously adjustable pressure to the wire electrode. The latter is pressed against the outer wall of the conduit, where it causes about the same friction as otherwise against the inner wall. Ideally, the feed force is adjusted so that the wire at the outlet of the conduit may be pulled or blocked with just two fingers (few Newtons). The wire feeder can then supply any quantity of wire with the least amount of force.
An electrical connection between RoboFeed and the main drive is not necessary. RoboFeed comes to a standstill by itself when the main drive stops and delivers the right amount of wire by itself when the main drive is running, up to wire speeds of 50 m/min. Even in welding processes with rapidly changing wire speeds, RoboFeed reliably delivers the required wire speed. If an electrical connection is still required to relieve the drive during long breaks, RoboFeed also provides this in any case.
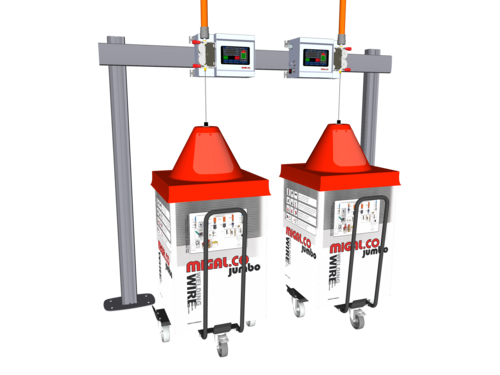
RoboFeed-WireManager has a powerful wire feed motor with 100 Watts of power at its drive shaft. It assists the main wire feed motor by supplying always sufficient welding wire even at large distances from the wire-pack to the welding robot. Additionally it records the wire consumption, warns when the remaining wire quantity is low, inserts the wire at a specific length, shows statistical data, provides a stopwatch and talks to other devices via MQTT or OPC UA.
It allows a liner length of more than 50 m and therefore makes the welding cell design more flexible. The forces in the wire feed system are significantly reduced which cares for less wire feeding problems and a more stable welding process. It can operate fully independent and saves the time consuming wire insert by hand during wire pack change.
- Quad roll drive
- RoboFeed - WireManager applies a constant feed force, no electrical connection to the welding power source or welding robot required, but possible
- Optional barcode reader to recognize quantity, item number, batch number and manufacturing date of the wire (VDA-label)
- Rejects wire pack change if wire item number is not correct
- Statistics function
- Shows remaining wire content with pre-warning and warning thresholds
- Signal output, email and SMS as end-of-wire warning
- MQTT protocol for IoT (batch, drum content, wire speed)
- OPC UA server for IoT (batch, drum content, wire speed)
- CANopen (currently internal)
- Liner length between wire pack and robot of more than 50 m
- Prepared for wall mount (brackets are included)
- Floor mount with optional stand
- Can be used with Rolliner NG, 3G, XL2 and with Softliner or Toughliner
- The panel can be rotated for vertical or horizontal wire feed direction
- Electrical interface (24 Volts) for Start/Stop and wire forward/backward
- Setup function for commissioning
- Jogging with wireless remote control (battery-free EnOcean), 2 speeds
- Automatic threading (setting of feed force and length)
- Wire retraction during threading if wire gets stuck
- Stopwatch function for wire length, weight, duty cycle
- Settings with PIN code
Technical data
Wire feed speed | 0 - 50 m/min |
Feeding force | 0 - 165 N |
Dimensions LxBxH | 440 x 255 x 170 mm |
Weight | 9.9 kg |
Wire diameter | 0.8 - 1.6 mm (larger diameter on request) |
Power supply | 115 - 230 volts / 50 - 60 Hz |