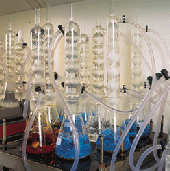
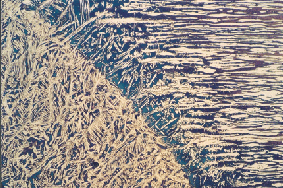
The choice of welding consumables is crucial to the result of the welding operation. It must give the required weld properties and ensure a crack-free weld. The key factor in the choice is, of course, the parent metal, but welding method can also influence the selection of filler metal. For surfacing, the welding parameters have to be considered as well.
Balanced composition
The composition of the welding consumable normally corresponds to that of the parent metal. For example, parent metal 304L (18% Cr, 8% Ni) is welded with a 308L filler metal (19% Cr, 9% Ni). In general, the contents of the main alloying elements - Cr, Ni and Mo - are higher in the welding consumable than in the parent metal in order to compensate for segregation in the weld metal.
Impurity levels, however, are lower in the consumable than in the parent metal in order to reduce the risk of hot cracking, and to obtain the best arc stability, fluidity and wetting properties. In standard austenitic welding consumables - 308L, 316L, 347 - hot cracking can in practice be eliminated by a chemical composition, which gives a ferritic solidification. A ferrite content in the consumable of about 10 % (10FN) is usually sufficient, unless dilution from the parent metal is excessive.
Variants of one and the same consumable
For most standard grades there are two versions available; one with normal and one with high silicon content. The chemical compositions have been adapted to suit the welding method.
The high silicon versions are recommended for MIG welding, because they give the best arc stability and smooth welds. In TIG and plasma-arc welding, the high silicon filler metals are not as advantageous as in MIG welding. Nonetheless, they are still preferred by many users. Thus we decided to have the LSi variantns on stock.
Simplified stock holding
For stock holding reasons, many fabricators use one consumable grade to weld several different parent metals. Molybdenum has been shown to give only positive effects, except in highly concentrated, hot nitric acid environments. Therefore, 316L consumables can normally used for both 316/316L and 304/304L parent metals. The simpler stock holding and the elimination of the risk of mixed material fully compensates for the potentially higher price for 316L consumables compared to 308L.