Quand l’aluminium est exposé à l’atmosphère, une couche d’oxyde qui consiste fondamentalement en Al2O3 en deux couches partielles l’une sur l’autre se forme immédiatement, à savoir
- une couche de base ou de barrière, quasiment dénuée de porosité, d’oxyde d’aluminium amorphe
- une couche de couverture poreuse et hydratée avec un bas contenu de cristallin d’hydroxydes d’aluminium et de bayerite.
L’épaisseur de la couche d’oxydes augmente avec le temps, la température et la disponibilité d’oxygène. Même une couche d’oxyde très mince qui présente une température de fusion de 2300° C et protège la surface d’aluminium d’une corrosion continue peut être poreuse et absorber de l’humidité.
L’état de la surface lors du soudage MIG et TIG influence
- La stabilité de l’arc (la présence d’oxyde d’aluminium est nécessaire pour un arc stable)
- La géométrie du point focal de l’arc
- La baisse de tension dans l’arc et de ce fait de la longueur de l’arc
- La géométrie de la soudure
- La qualité de la soudure
- La capacité de reproduction du processus surtout pour la soudure automatique
En raison de l’épaisseur extrêmement fine, en nanomètres, de la couche d’oxyde, il est difficile de la mesurer dans la pratique.
Souvent, il ne reste que la possibilité d’éliminer entièrement la couche d’oxyde par des méthodes chimiques (décapage) et d’obtenir une épaisseur définie par un stockage à des conditions temporelles et d’environnement contrôlées.
Il faut d’ailleurs remarquer que la densité de l’oxyde d’aluminium par rapport au métal est plus élevée. En ce qui concerne l’acier, les oxydes ont un poids inférieur à celui du métal et pour cette raison ils flottent à la surface lors de la fonte. Les oxydes d’aluminium, par contre, descendent dans le bain et peuvent causer des inclusions d’oxydes.
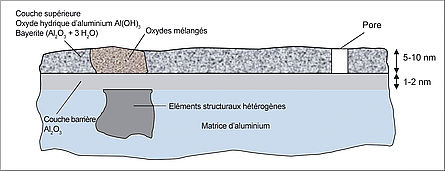