Aluminium immediately forms an oxide layer when exposed to the atmosphere which basically consists of amorphous Al2O3 in 2 partial layers on top of each other namely
- a nearly pore free base- or barrier layer of amorphous Aluminiumoxide and
- a porous and hydrated cover layer with low crystalline contents of Al-hydroxides and Bayerite.
The thickness of the oxide layer increases with time, temperature and availability of Oxygen. Even though the oxide layer is very tight, has a melting temperature of 2.300° Celsius and protects the Aluminium surface from further corrosion it can also be porous and pick up humidity.
The surface condition of Aluminium influences with MIG and TIG-welding
- the arc stability (a stable arc requires the presence of Aluminium oxide)
- the geometry of the arc focal point
- the voltage drop in the arc and therefore the arc length
- the geometry of the weld
- the quality of the weld
- the reproducibility of the process in particular with automatic welding
Due to the extremely small thickness of the oxide layer within few Nanometres it is hardly measurable under practical conditions. Hence, the only remaining possibility to obtain a defi ned oxide layer is to completely remove the old layer by chemical processes (pickling) and by storing under controlled conditions (environment and time). Further remarkable is the fact that the density of Aluminium oxide in comparison to the metal itself is higher. With iron (steel) the oxides have a lower weight than the metal and therefore fl oat on the surface of the molten pool. With Aluminium the oxide sinks into the molten metal and may cause oxide inclusions.
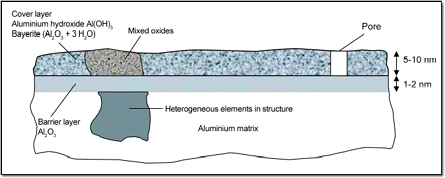