Amongst all gases only Hydrogen can be solved in Aluminium. Compared with the solubility of gases in iron alloys, however, the quantity is rather low.
The solubility of Hydrogen in Aluminium depends on the content of alloys and on the temperature. The solved quantity furthermore depends on the availability of Hydrogen, which is usually given as the partial pressure and indicated in Millilitres of the solved gas per 100 Grams of metal. (1013 mbar and 0° Celsius; 1 ppm = 1,1124 ml/100g)
As the solubility of Hydrogen in Aluminium suddenly decreases at a temperature of approx. 600° Celsius during cooling it often comes to porosity caused by frozen gas bubbles. With pure Aluminium the tendency to porosity is most serious, whereas it is lower with alloys. This is due to a smaller leap in the solubility of Hydrogen.
These circumstances lead to the fact that the presence of porosity with MIG-welding of Aluminium is nearly unavoidable.
Pores have negative implications on the static and dynamic strength of welded joints and can be disturbing anyway. Machining the surfaces opens pores which don´t look nice and may reduce the adhesion of paint.
Inspectors have trouble to determine the level of acceptable porosity and both fabricators and customers consider it as just poor work.
The basic solution to this problem is to keep the level of available Hydrogen as low as possible. Generally a Hydrogen content of approx. 0,2 to 0,3 ml/100g is considered to be the maximum permitted level in order to get low porosity. This value is exceeded under practical conditions quite frequently. Sources of Hydrogen are base material, fi ller material, shielding gas and atmosphere. Clean storage- and fabrication conditions, preparation of the surfaces and prevention of all other sources of Hydrogen is the most important rule.
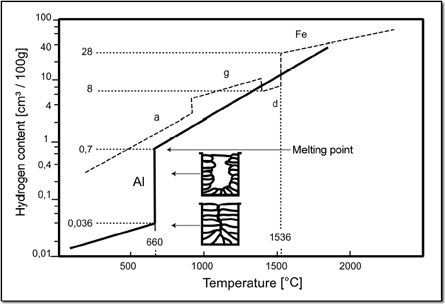
